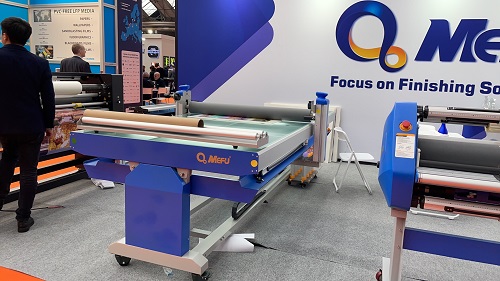
1600mm width flatbed laminator with side tray in the USA
In addition to the large capacity and side tray design, the flatbed laminator MF-B4 has other attractive advantages: Tilted Table & Safety Glass, LED Illumination and Media roll holder on bed end, which can help to solve many problems in the laminating process and make the whole laminating process more efficient.
In a small town in the central Southwest of the United States, there is a small store specializing in printing services for thirty years, this small store has always been the first choice of local residents of the printing business, and recently this small store has once again become very famous, and what is the reason for this?
Well, it’s because they’ve supplemented their print business with a new laminating machine from a laminator manufacturer, a 1600 mm wide flatbed laminator with side trays that is revolutionizing the way they handle large print products.
With a generous 1600 mm capacity, the flatbed laminator MF-B4 is able to cover large areas of material while maintaining high quality and precision. The side tray design is another highlight of this flatbed laminator, allowing easy access to both thin paper and heavy vinyl sheets. The side tray makes the laminating process not only smoother, but also significantly improves efficiency by reducing manual labor time and the possibility of errors.
In addition to the large capacity and side tray design, the flatbed laminator MF-B4 has other attractive advantages: Tilted Table & Safety Glass, LED Illumination and Media roll holder on bed end, which can help to solve many problems in the laminating process and make the whole laminating process more efficient.
FAQ
What if the lamination thickness is not uniform?
Uneven film thickness during the lamination process will greatly affect the quality and aesthetics of the product if this happens it is likely to be due to the following reasons:
1, Whether the laminating roller is cleaned regularly or not, the dirt of the roller may lead to uneven thickness of the laminating film.
2, Too tight or too loose tension may lead to uneven thickness.
3, Check the roller pressure setting of the laminating machine, incorrect roller pressure may also lead to uneven thickness.
What is the reason for finding bubbles on the surface of the material after laminating?
1, Too high a temperature may lead to bubble formation, which can be improved by adjusting the laminating temperature.
2, Ensure that the humidity of the working environment is appropriate, too high or too low humidity may lead to bubble formation.
3, Check the quality of the laminating film rolls, low-quality film rolls may contain air bubbles.